Case Study
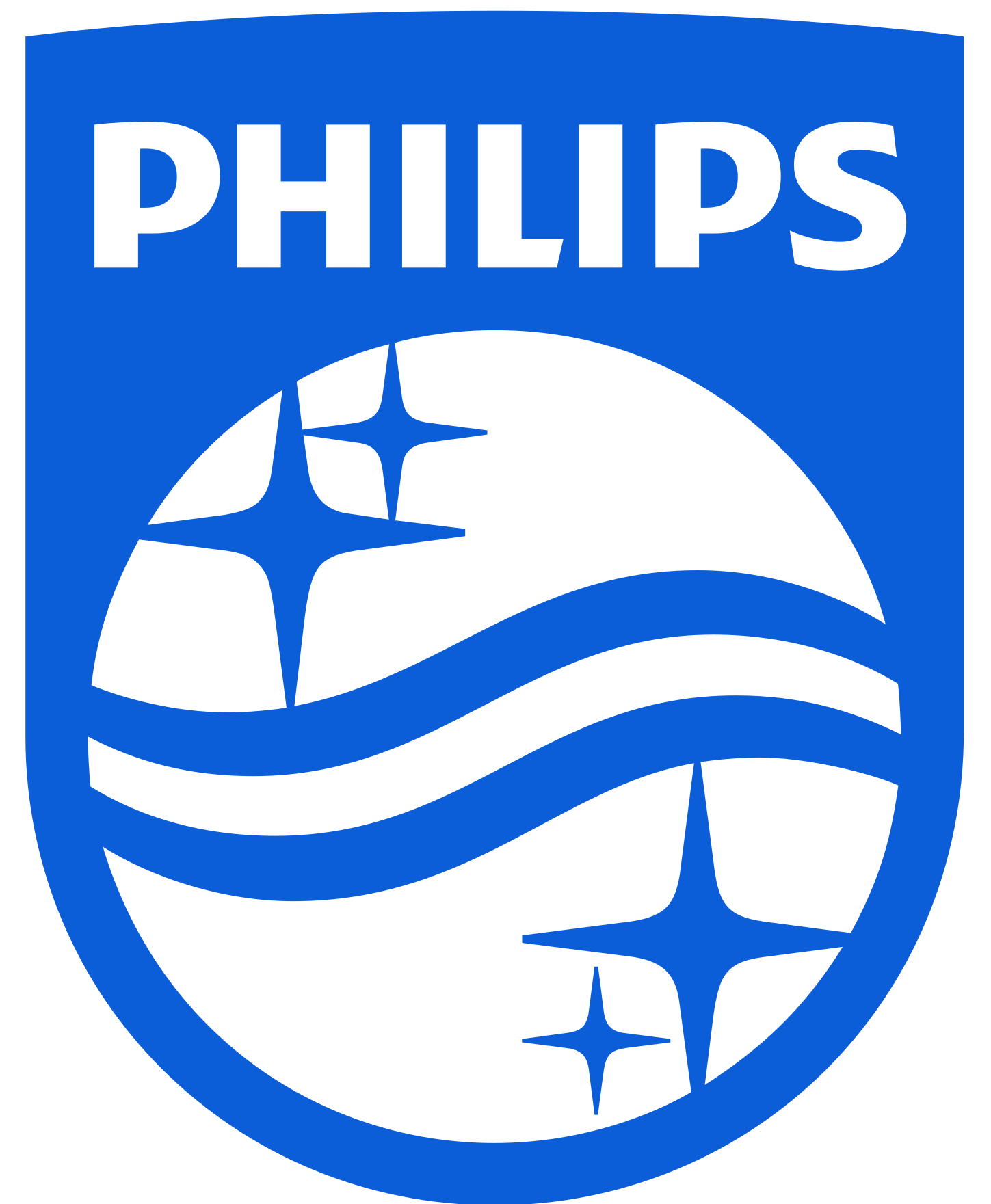
The successful faults prediction in Philips
About Philips C.L.
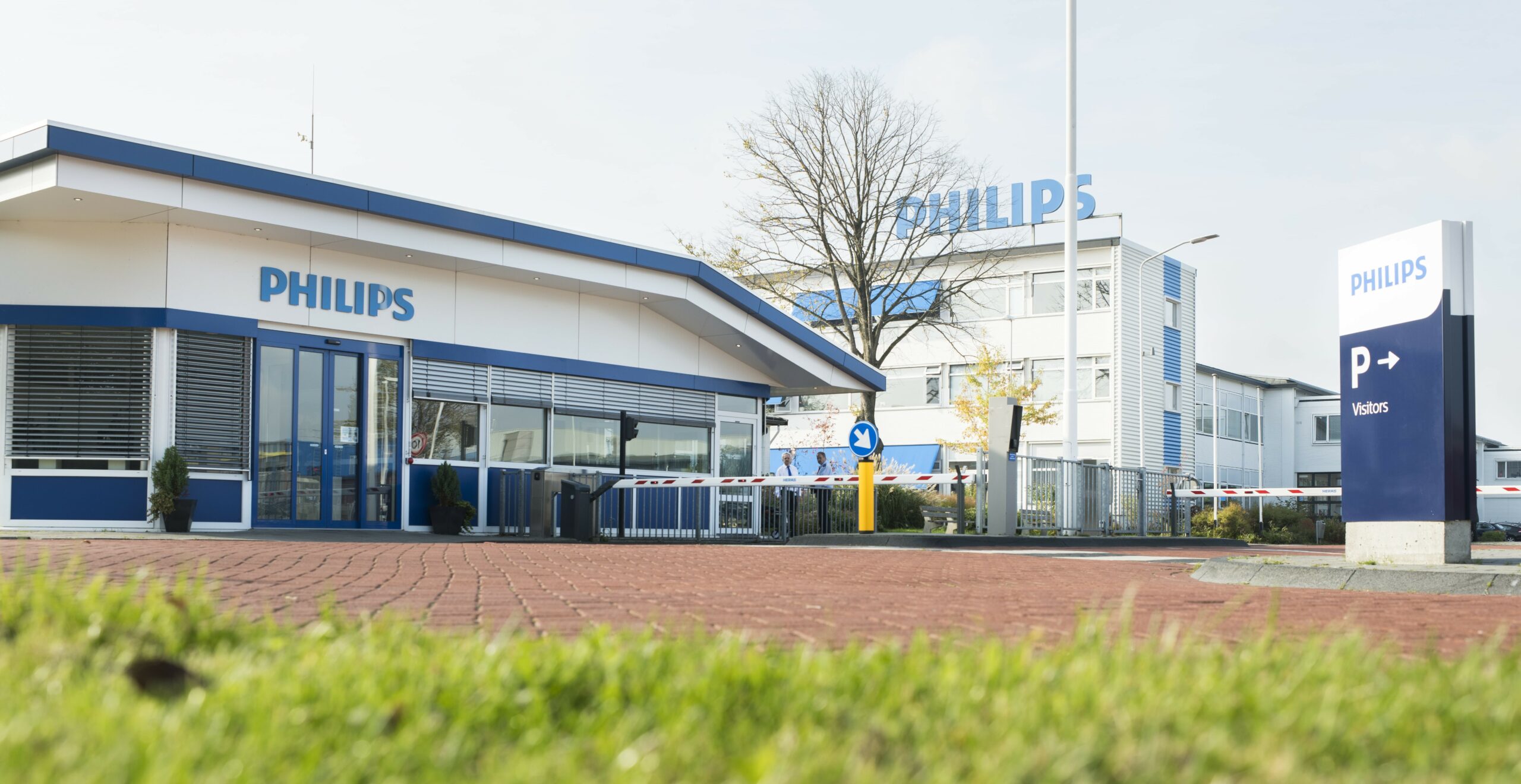
Addressing challenges
The need
Sibyl's journey at Philips starts by its implementation at the electric shaver manufacturing plant. It was prompted by Philips' aim to fundamentally address breakdowns and quality problems in the presses of the metal cold forming line before occurrence.
Choosing Sensors
After the project team's analyses, the selected prediction models relied on acoustic signals (ultrasound). The whole sampling procedure of the high-density signals has been achieved by placing seven (7) sensors on the head of each press. It is worth noting that thousands of point measurements are selected from each stroke of the press.
First indications
In a short time, Sibyl's models began to perceive with great clarity the "pulse" of the machines and give their first predictions. The successful results in identifying different failure modes and quality problems strengthened the acceptance of the production staff to adopt it in their daily work routine.
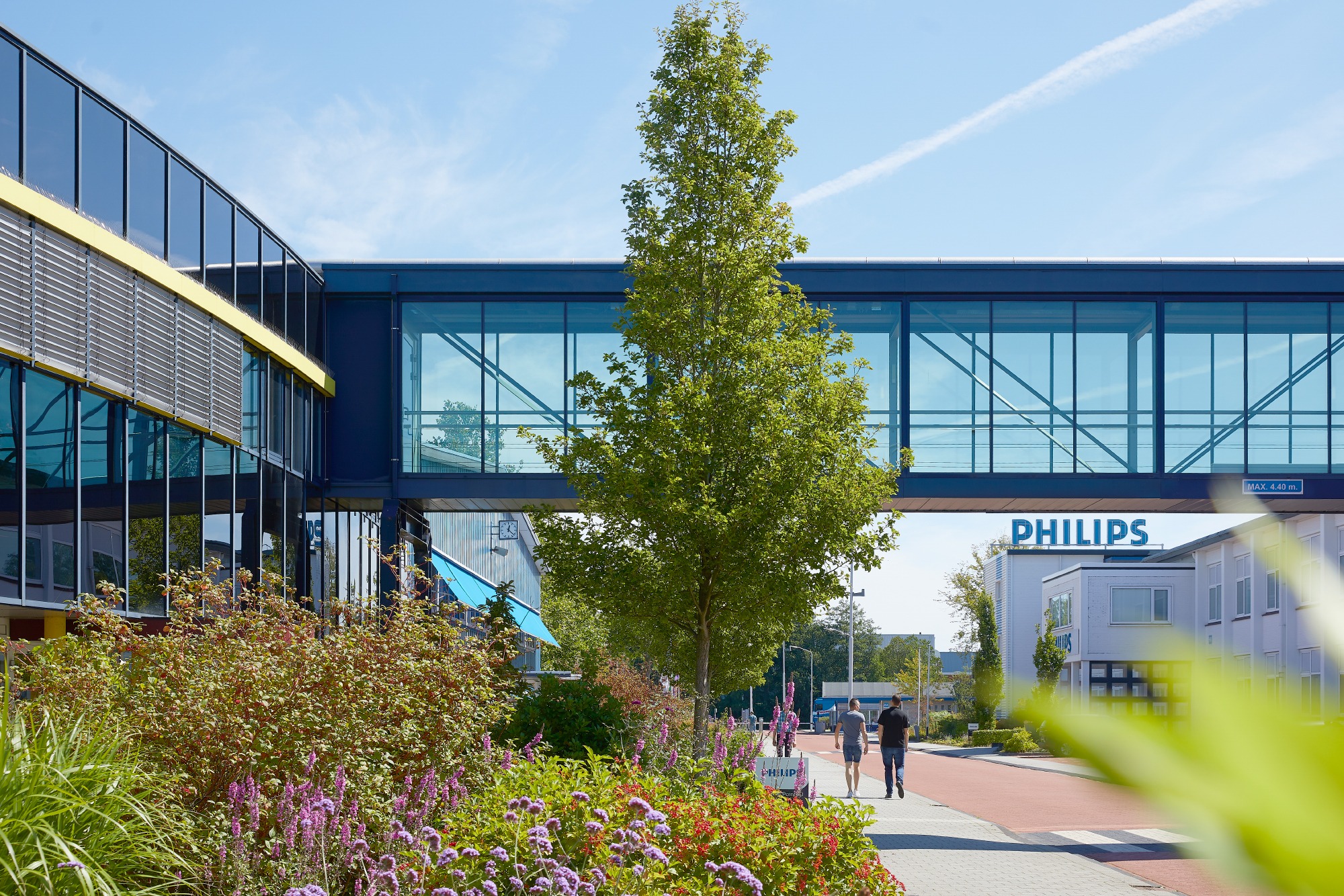
Results
Robotic Arms
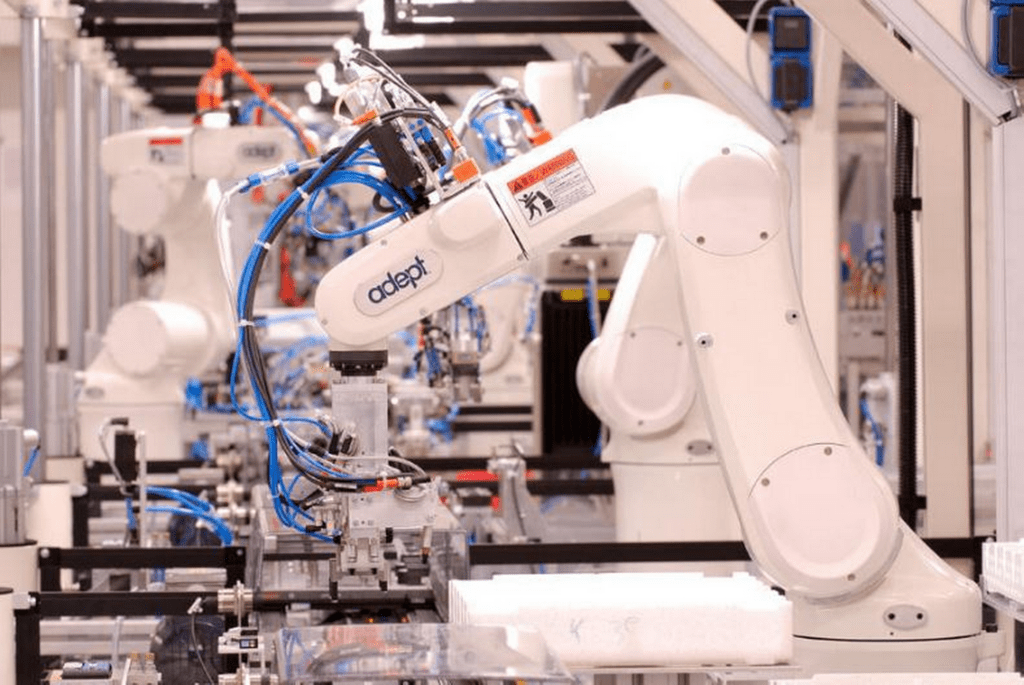
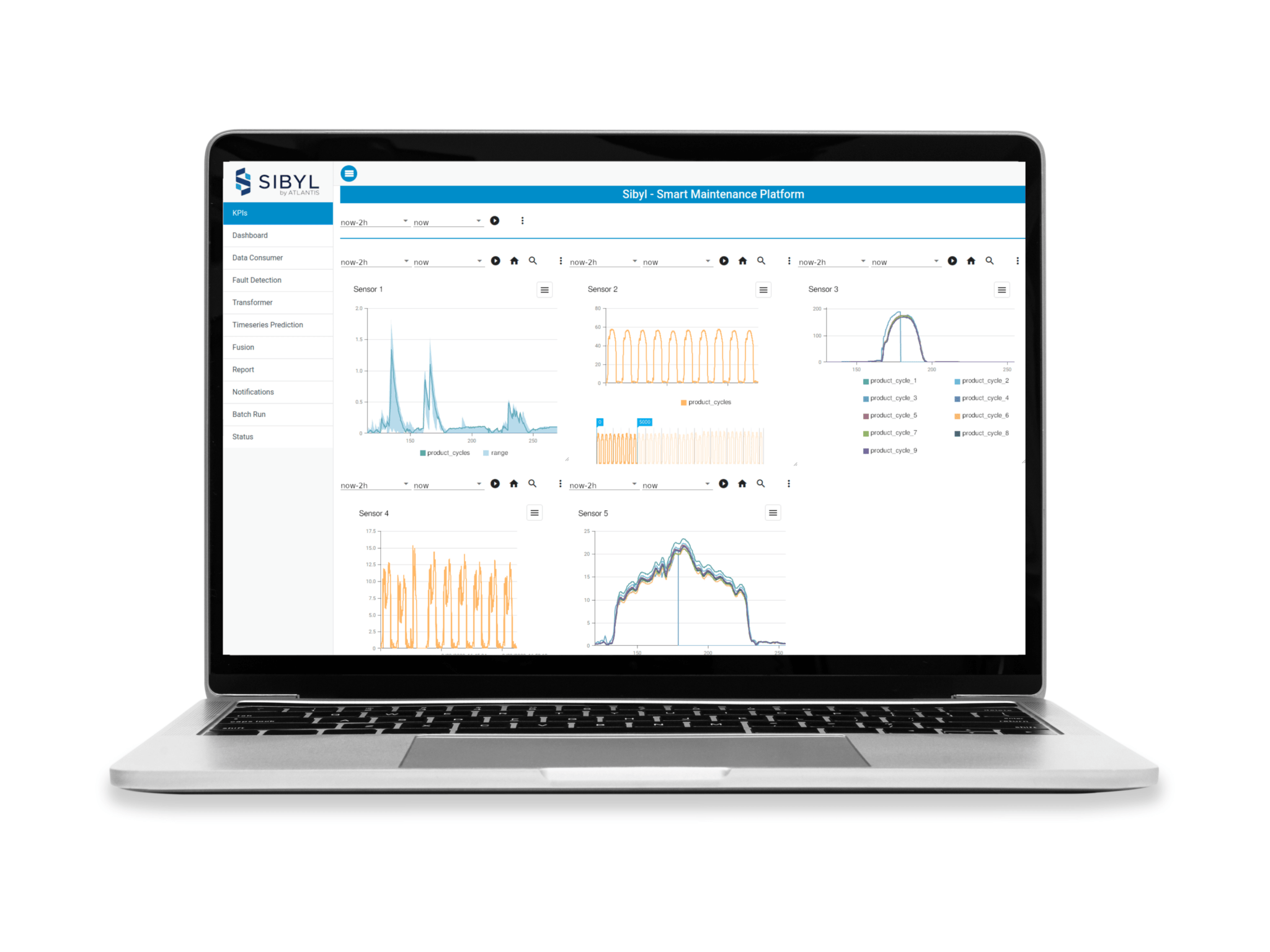
User Interface
Joint Working Group
It is worth mentioning that a critical point of added value for the successful implementation of Sibyl was the joint working group between Philips’ engineers and Atlantis Engineering’ data scientists. The high-end project is reflecting the quality of the executives and teamwork, while Atlantis’ frequent and organized on-site meetings allowed rapid interpretation of outcomes and fast training of Sibyl’s models. Finally, the transfer of know-how by DataLab laboratory of the Informatics department of the Aristotle University of Thessaloniki (AUTh) was valuable for the project.
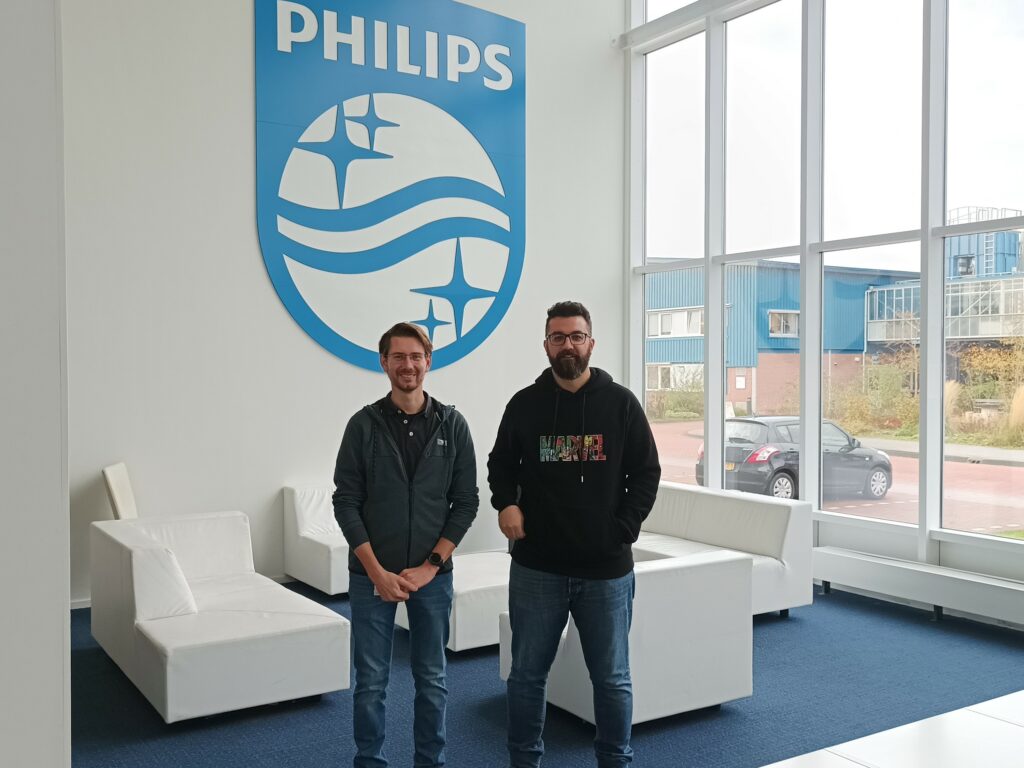
Testimonial
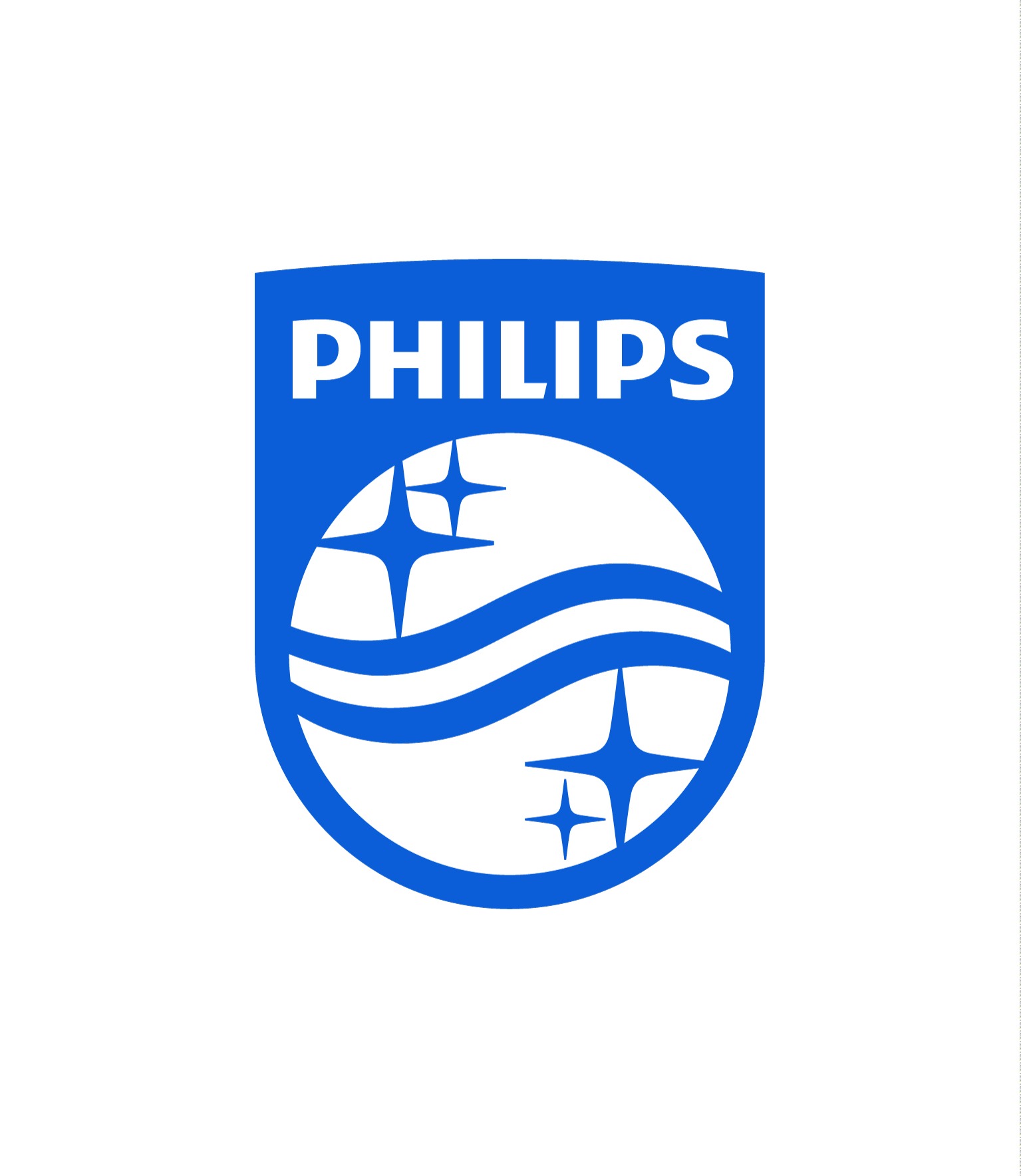
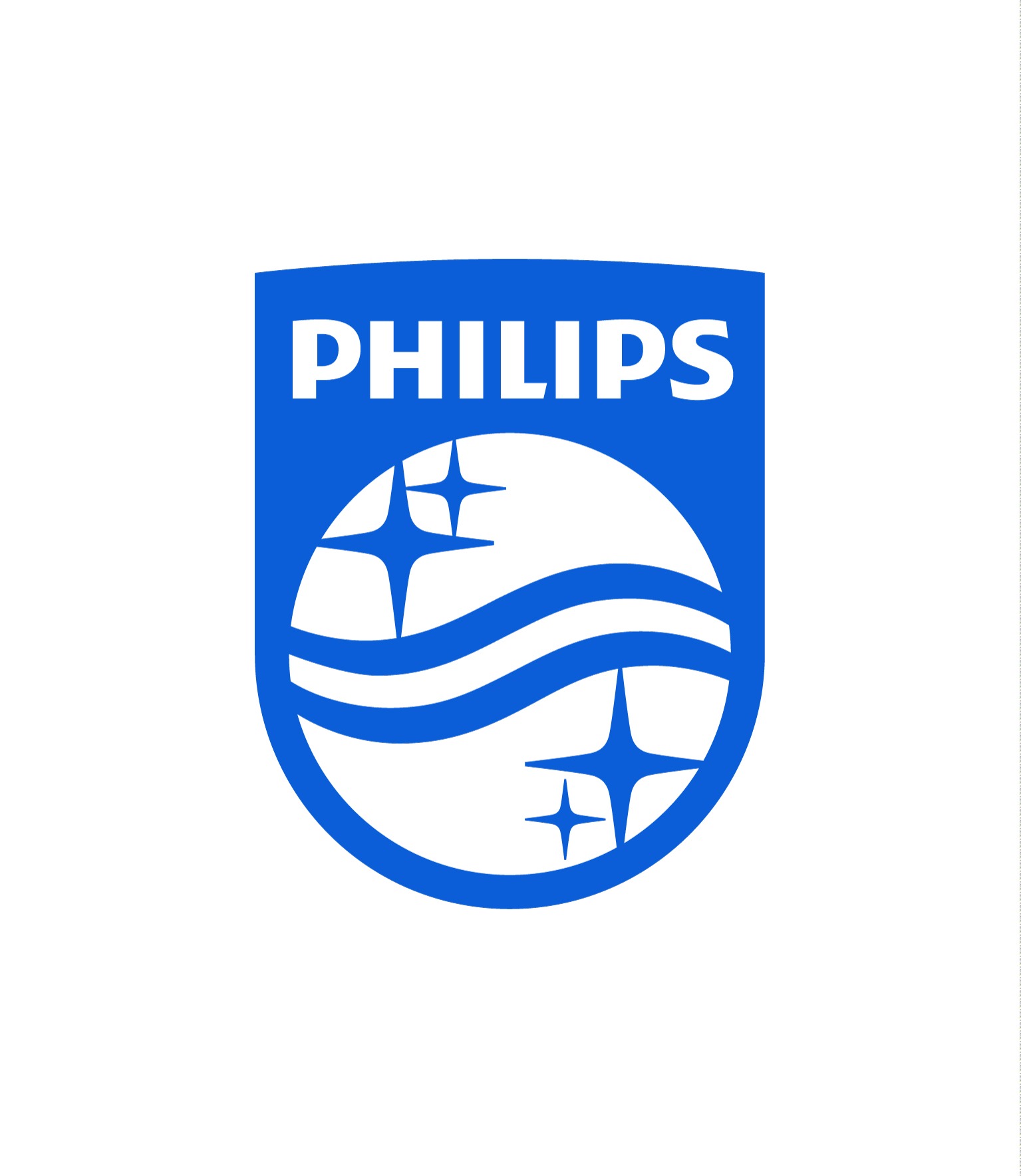
Results - Benefits

Faults forecast up to 72 hours ahead of the incident time
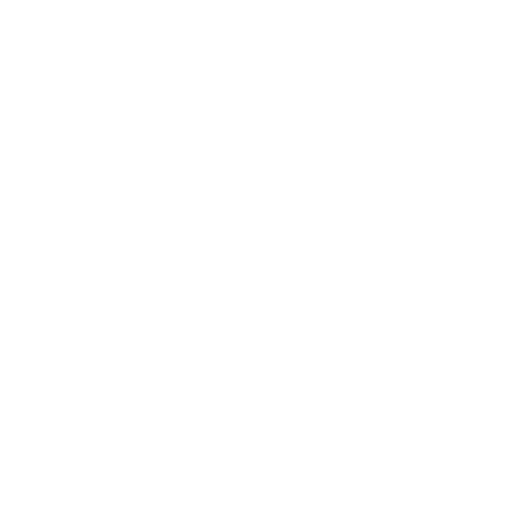
On-time diagnosis of numerous faults, in more than 60% of cases
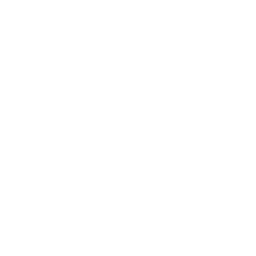
Prevention of press downtimes, especially important during understaffed night shifts
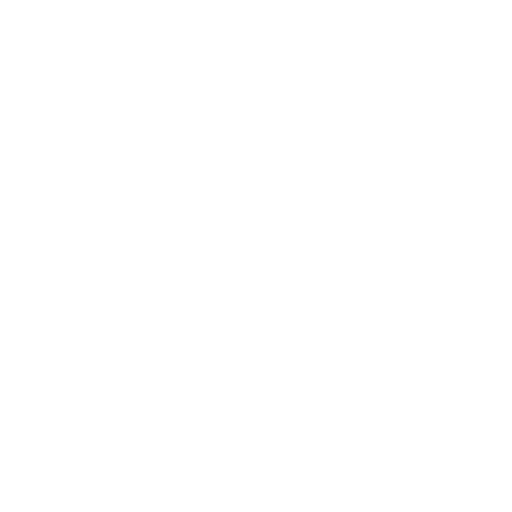
Time leeway for the engineers to plan the repairs
Contact Us
Right time to simplify your maintenance procedures
By submitting this form, you agree to our Privacy Policy and consent to the collection and use of your personal information for communication and marketing purposes. We may contact you via email or other methods for promotional offers, updates, and relevant information. You can opt-out at any time.